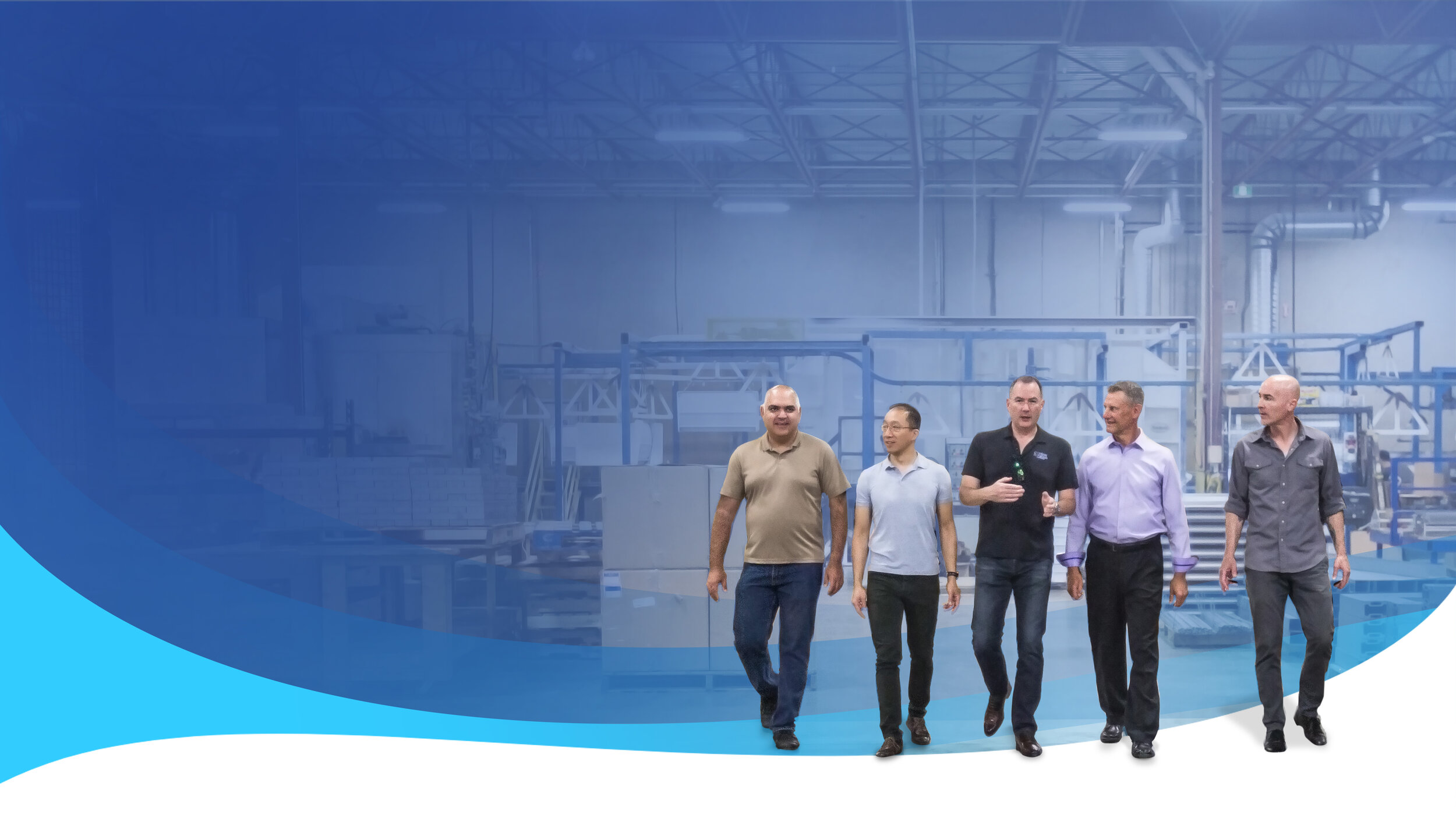
Blog
MISys Manufacturing - Custom Fields
Data that is not included as a standard field in a MISys table can potentially be added as a custom field.
For example, Bills of Material often have an associated documents including diagrams that provide step by step instructions for production. If the document is specific to an operation, a custom field can be added for the network path of the document that can be accessed from the Bill of Material or Manufacturing Order Routing tab.
MISys Manufacturing – Calibrated Measurement and Inspection Tooling Records
Manufacturers rely on measurement devices for production and inspection. Some of those devices may be calibrated within a Quality Management System (QMS) and therefore need to be logged to maintain tooling records. MISys has a Tooling register that works well to maintain the Calibration requirements and includes reports that notify of upcoming maintenance due dates for calibration.
MISys Manufacturing – Comparing Stock Quantities on two dates.
For the purposes of maintaining and tracking physical inventory, MISys has a utility in Stock Control/Stock Movement that provides capture of an inventory snapshot record.
MISys Manufacturing – Accessing the MISys EXT web app through the MISys desktop
The MISys EXT web interface is particularly effective when used in combination with MISys the desktop. To enable access to MISys EXT through the MISys desktop, go to Administration/Company Profile/Website and click the check box ‘Display MISys Manufacturing EXT in Info Center’.
MISys Manufacturing – Database Confusion
When there is more than one database available in the system (e.g., Live/Production & MITESTCO/Test database), there is a risk of logging into to the wrong database and transacting there.
MISys Manufacturing – Determine Inactive Items using a Master Production Schedule.
Knowing which items are required for future production is the foundation of good materials management. Similarly, knowing which items are not required allows for setting those items as inactive and potentially purging them. Doing so provides value because it directs organizational efforts on the needed items and away from what is not needed. A couple related examples are that of stockroom space can potentially be freed up and balance sheets will become more accurate.
MISys Manufacturing – Lead time Confusion
Why are there multiple fields in MISys to enter Order Lead and what does ‘Order Lead’ refer to?
Let’s start with the basics; ‘Order Lead’ in MISys is refers to the time that is needed for purchased items to arrive to the shipping location after placing the Purchase Order (PO) with the supplier. These are calendar days (7 days/week).
MISys Manufacturing – Checking for Recursive BOMs
As per MISys, “a Recursive BOM is a bill of material that includes itself as a component”.
MISys Manufacturing – Deleting Obsolete Items
Over time, the master files in MISys increase in size and can slow down the system. It’s surprising to find out that many times, master files that were created for a purpose were never used. This creates unnecessary data pollution and can easily be rectified.
MISys Manufacturing – Changing Bill of Material Components – Add or Remove
Following from our “Changing Bill of Material Components – Replace” blogpost , in this post we will cover how to ‘Add’ or ‘Remove’ Bill of Material (BOM) components to/from existing BOMs. Adding a component to a BOM will allow the user to add a new item with a specified quantity to selected BOMs. Removing components will delete an item that’s currently in selected BOMs.
MISys Manufacturing – Changing Supplier Numbers & Location Numbers
Sometimes it might be necessary to change the Supplier No. or Location No. in MISys in much the same way as it might be necessary to change the Item No. The good news is that the process to achieve this is the same as Changing Item No., as was outlined in my previous two blog posts (see Changing Item No. - Part 1 & Changing Item No. - Part 2).
MISys Manufacturing – Stock Unit vs. Purchase Unit
MISys allows users to set a specific unit of measure for each supplier of an item that might be different than the Stock Unit of Measure (UoM) of that item. This is referred to as the Purchase Unit of Measure (PUoM).